What’s Your Stockout Risk?
Dec 2, 2024
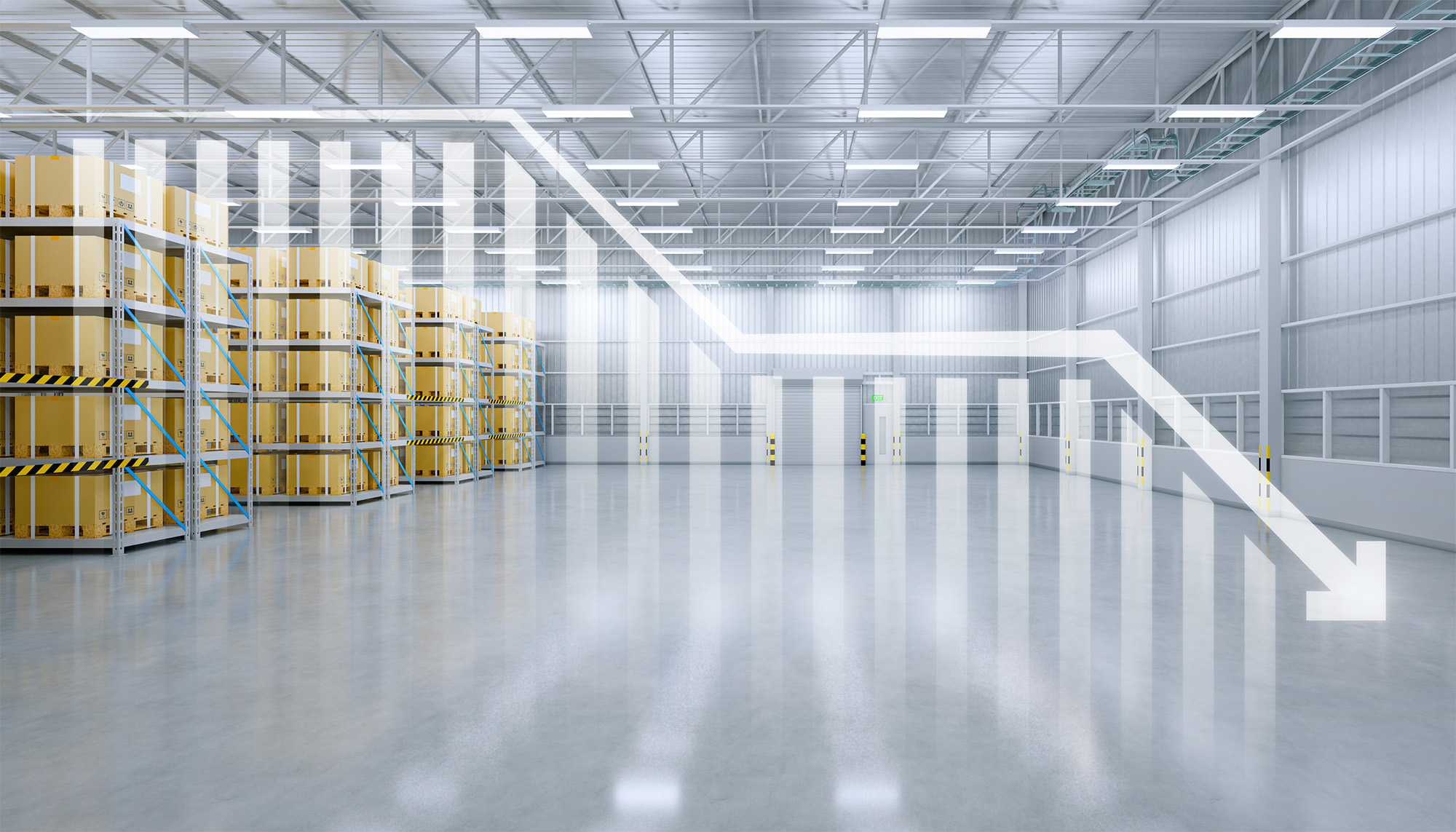
Parts stockouts are a costly challenge that today’s manufacturers face. A stockout occurs when a critical part for running your operation is not available in your inventory and is also in demand. Lengthy production delays, increased costs from expedited stock, and potential audits from data inaccuracy are just some of the impacts on overall equipment effectiveness (OEE).
Not having spares for your most critical items during testing, ramp-up, or production will reduce the integrity of your automated manufacturing system. Adam Mohammed, Spares Solutions Specialist, Service & Parts at ATS Corporation (ATS) prepares recommended spare parts lists (RSPL) for manufacturers. He advises on the potential risks for assets if required parts are not at stock locations.
In his experience, understanding and observing lead times is imperative for sustained operational productivity:
“I think the main issue from the experience I’ve gathered in talking with customers at ATS is really inventory management. If manufacturers don’t understand what they have or what they need, this will impact what is available. Sometimes, it’s simply not understanding the risks until they actually happen.”
Adam Mohammed, Spares Solutions Specialist
Manufacturing stockouts can increase today’s already high operational costs, especially those resulting in downtime. An article titled The Monthly Metric: Unscheduled Downtime by Dan Zieger in Inside Supply Management Magazine discusses how to calculate the cost of operational disruptions:
“Unscheduled downtime can be calculated by logging the duration of each shutdown that falls outside of planned maintenance/upgrades and scheduled breaks. Measured on a monthly basis, for example, it can be calculated as a percentage of expected production time. A higher percentage indicates a need for improved preventive maintenance or equipment reliability.”
The article also states, “This dynamic can be exacerbated at smaller businesses and suppliers, which are more vulnerable to financial strain and inventory stockouts.”
If you’re not considering stockout risk, you’re increasing your risk for downtime and compromising production targets. The most common causes of parts stockouts are poor inventory management and weak supplier relationships.
Are you at the top of your supplier’s priority list?
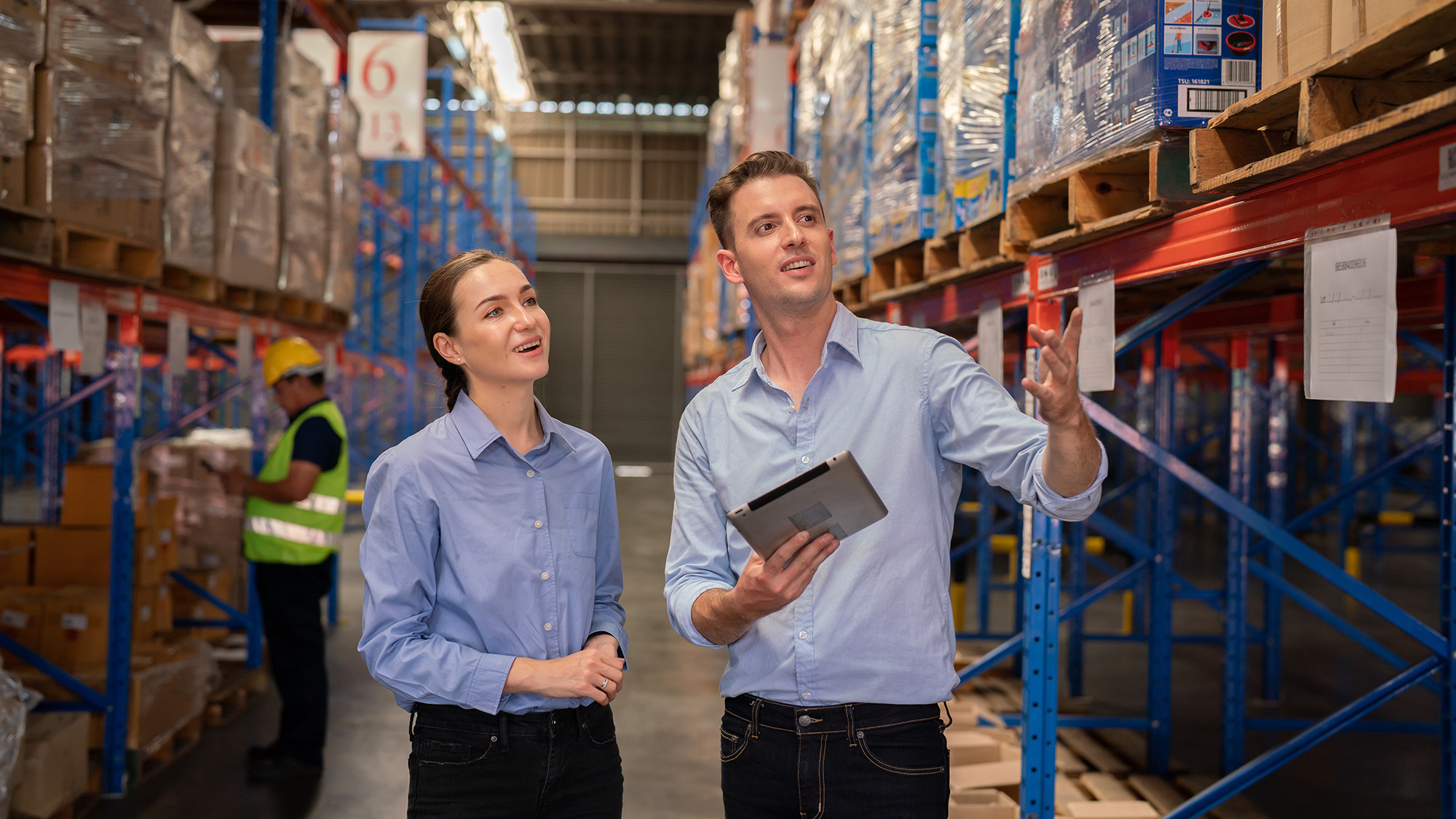
Strong supplier partnerships with good communication, reliable service, and lead times can assist manufacturers in improving visibility of their parts inventory. These important relationships can significantly benefit your operational performance and are exemplified when suppliers prioritize your needs. Accurate information from your supplier will improve your inventory management program.
Areas where supplier information can impact manufacturers’ risk for parts stockout:
- Accuracy of lead time
- Purchase order reviews and acknowledgement
- Limited communication on the status of orders
- Supplier stocking and capacity
Capture stockout risk in your inventory management plan
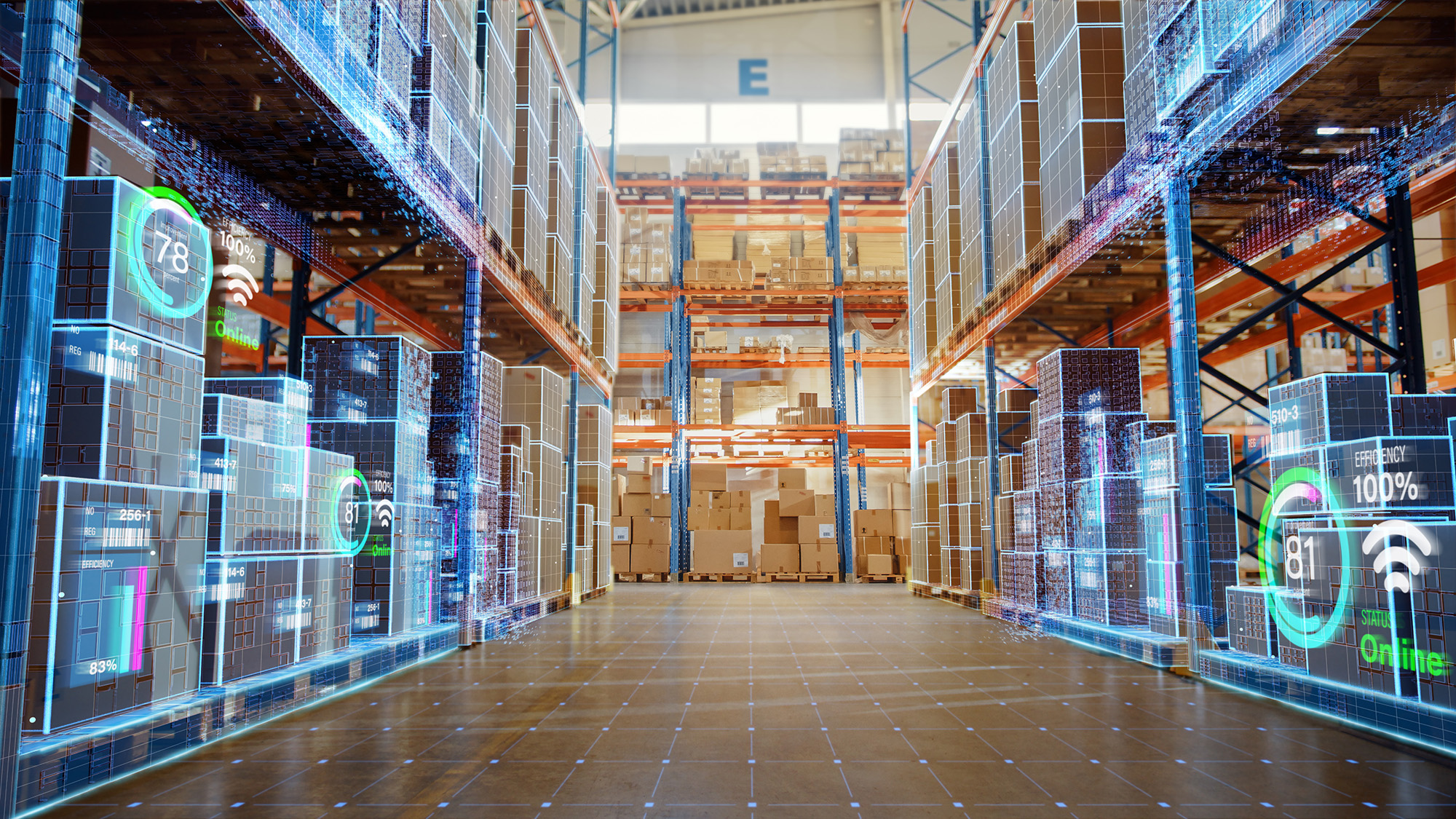
Understanding parts consumption patterns in your inventory is integral to keeping your operation at peak performance. This information identifies parts requiring frequent replacement and the cadence at which this maintenance should be planned. Forecasting is essential to ensure spares are on hand to mitigate stockout risk. Items to watch out for are those prone to wear and tear like gears, grippers, and chains. These are continually in motion and in constant contact with other machine equipment.
Keep an eye on stock levels for costly, high lead time items including electromechanical parts such as motors and smart electrical components like PLCs and HMIs. Last-time-buy items are also risky because they’re high in demand and likely to become unavailable.
Including these criteria in your inventory planning gives you options to strategize budgeting for high- and low-risk items. Information on inventory for parts stocked around the globe may be beneficial to access a part in the event of a manufacturing stockout. Your plan also needs to consider warehousing logistics like limited space that can impact stocking options. Understanding warning signs can help you mitigate stockout risk by reviewing important aspects that can impact your manufacturing performance.
Warning signs that a stockout may occur in your operations
- Supply chain constraints: unexpected delivery delays may impact the replenishment cadence for stock inventory.
- Increase of demand and obsolescence: if there is a known last time buy for equipment from suppliers, demand may spike for flagged obsolescence of material.
- Manufacturing delays: global economics and events may impact production with lower output of material from suppliers.
- Questionable inventory management: consistently inaccurate inventory stocking leads to a high risk of a parts stockout.
Mitigate the risks of unplanned downtime with accuracy
The accuracy of the information in your plan is fundamental and should include best practices for recording and updating information like employee accountability and scheduled process reviews.
“Resulting from poor data integrity, customers may be overstocking and others not stocking enough. Reliable software can contribute to data integrity by tracking and providing analytical insights on purchasing and consumption behaviors and automatically determining reorder points based on a carefully developed safety or strategic stocking plan,” informs Adam Mohammed, ATS.
Inventory cycle counts are often an overlooked requirement for validating your data. Things such as unlogged, defective, misplaced, or miscatalogued parts contribute to data inaccuracies and can only be solved through physical inventory counts.
Better parts inventory management starts with self-assessment
Conducting a self-assessment is a good way to get started on developing a stockout risk mitigation plan. This includes identifying parts at risk and evaluating lead times, considering supplier dependability, and obsolescence planning. Engaging the plant operations team for information on potential bottlenecks is useful to understand your parts status. Team members integral to inventory processes include the inventory manager, maintenance technicians, supply chain, and warehousing.
4 self-assessment tips to identify risks
- Identify safety stock levels in your planning to ensure buffer stock for when you need a part.
- Invest in inventory management tools to monitor stock and provide alerts on stock levels and reorders.
- Perform cadence reviews of stock inventory by auditing the frequency of consumption. If parts are not used frequently or highly consumed, adjust the stocking strategy.
- Maintain healthy supplier relationships with open communication on priced deals, on-time delivery, priority service, and programs for repeat buyers.
Increase operational performance
Maintaining a reliable manufacturing inventory management program over the long term improves your production goals. Here are some best practices:
- Understand what parts are critical to maintaining production operations.
- Reevaluate min/max ordering of stock based on lead time data.
- Ensure good documentation practices and consistent data integrity for auditing in/out inventory.
- Identify gaps in forecasting, stocking strategies, and supplier relationships for continuous improvement.
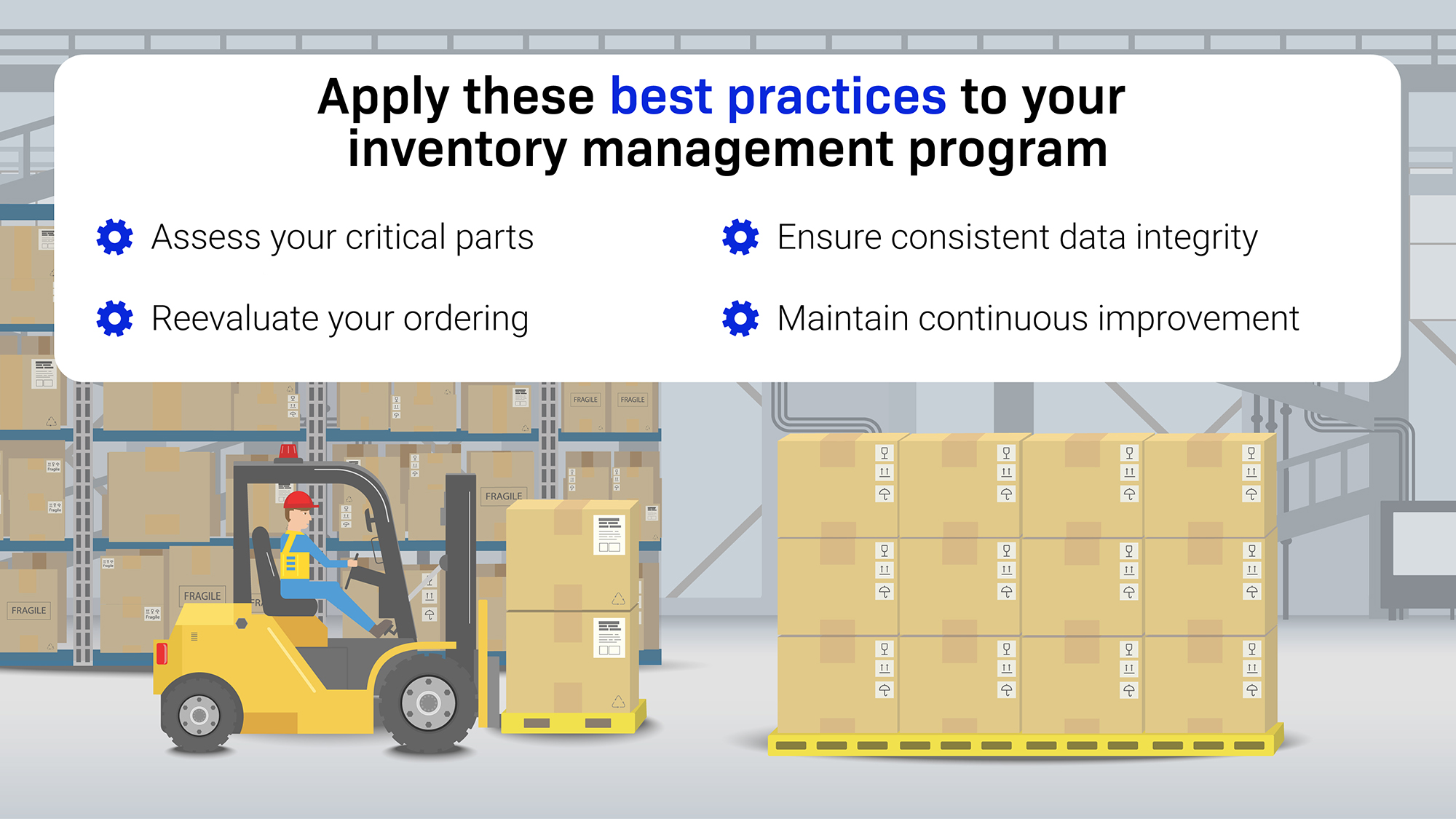
Closing thoughts
The factors increasing the likelihood of manufacturing stockout are essential to know for predictive performance in your operation. Other industrial factors to consider are new technological innovations contributing to obsolescence. Global economics and environmental impacts like disasters can also impact budgets by increasing costs for natural resources used in parts. It is important to monitor global events that may disrupt the supply chain and affect demand.
Both internal inventory management practices and external supplier relationships can mitigate parts stockout risks. This preventable event affects the entire supply chain, including compromising order fulfillment for customers depending on your products.
Developing and maintaining a strategic inventory management plan with appropriate stock levels can be a significant investment in time and resources. However, compared to the lost revenue of downtime, the investment is well worth it. So, what’s your risk?
To learn more about mitigating stockout risks, connect with an ATS service representative.
Source:
Zeiger, Dan. “The Monthly Metric: Unscheduled Downtime.” Inside Supply Management Magazine. August 27, 2024.