Optimize Your Parts Inventory to Reduce Obsolescence Risk
Jan 13, 2025
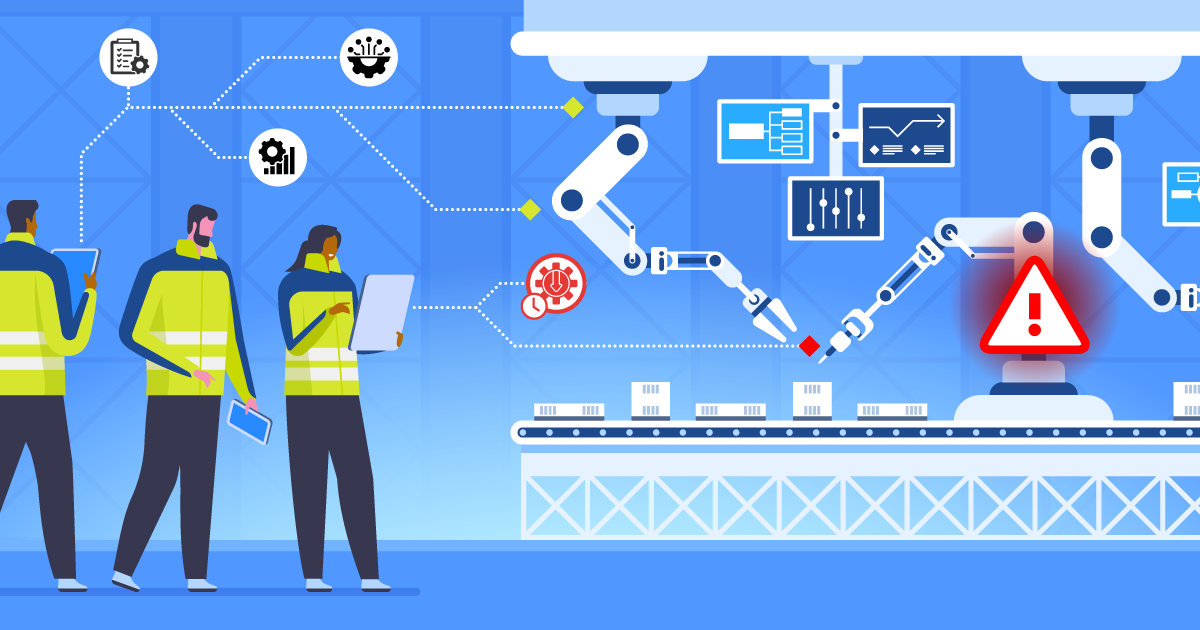
Why risk downtime when you can be prepared for obsolescence? In the fast-paced world of manufacturing, unplanned downtime is a significant drain on resources and operational performance, leading to substantial production losses. Obsolescence risk is inevitable and occurs in new and old equipment. Your operation is at high risk for downtime when an original equipment manufacturer (OEM) decides to no longer produce a critical part required to run your production line and there is no available inventory of that part or plan to replace it.
Proactive maintenance practices such as planned preventive maintenance (PPM) can go a long way toward reducing the occurrence of unplanned downtime events. However, when these events involve obsolete parts that are difficult to source or replace, the disruption is often prolonged. This is why a strong inventory management program and budget is imperative to manage obsolescence risk. Otherwise, the financial impact of downtime events can be catastrophic.
The high cost of unplanned downtime
The immediate cost of unplanned downtime is the failure to meet production targets, resulting in lost revenue. Longer-term consequences include customer dissatisfaction, which can result in the search for a new supplier.
Manufacturers caught off guard by equipment failures or outdated technology also end up paying for expensive emergency repairs. These repairs can divert maintenance and operations teams from their regular duties, which disrupt other critical processes within the plant. Additionally, the urgency of the situation may require bringing in specialized technicians from outside service providers, incurring significant labour and travel expenses.

Addressing the inefficiency of reactive solutions
Without a proactive strategy, manufacturers are forced to implement “band-aid” solutions. These quick fixes might temporarily resolve the issue but can also slow down production and cause further damage to equipment. There’s also a risk to employee safety, as obsolete components typically do not meet current standards and can impact the safe operation of machinery. This reactive approach not only hampers efficiency but also increases risks to employees and machines, potentially prolonging the duration of future downtime events.
Is your manufacturing operation in jeopardy of an ‘all bets are off’ situation?
Obsolescence in manufacturing occurs when a component that was part of the original design of the system is no longer being produced. If you don’t have the obsolete part and can’t get it, it is likely that ‘all bets are off’, and a quick fix is unavailable. This unpredictability isn’t worth it and can be resolved with a thorough inventory management strategy.
The International Institute of Obsolescence Management offers insight into obsolescence management and defines it as “the need to understand why this has happened and to plan and mitigate these instances in the future. Obsolescence concerns materials, components, processes, skills, and software. It can occur in all stages of the equipment’s life cycle such as development, design, production, and in service. It affects components which need to be maintained for long periods of time.”
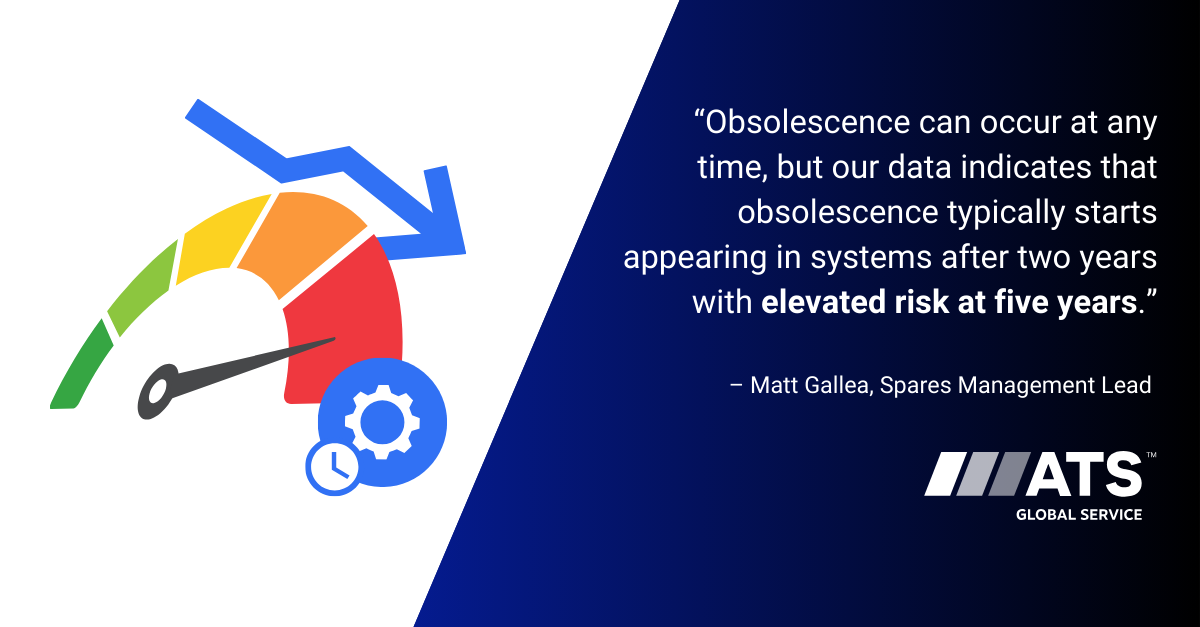
Your operations team, including the plant manager, maintenance technicians, system leads, and operators, are all integral resources in providing the wide array of data required for your plan.
Matt Gallea, Spares Management Lead (ATS), has 20 years of experience at ATS, starting as a Machine Tool Builder. He has held roles in Field Service, Assembly Management, and Service Project Management while supporting divisions and programs in North America and Asia across life science, automotive, nuclear, and solar industries.
For the past five years, Matt has specialized in obsolescence management and advises:
“Obsolescence can occur at any time, but our data indicates that obsolescence typically starts appearing in systems after two years with elevated risk at five years. Understanding this information can impact budgets for obsolescence management, an area that is often overlooked but crucial for preparing for obsolescence events. This will provide funds for when Last Time Buy (LTB) parts need to be purchased, or when immediate upgrades and redesigns are required.”
Manage parts obsolescence risk with a strong inventory management plan
Managing parts inventory effectively is crucial for manufacturers to avoid the pitfalls of obsolescence. Balancing short-term and long-term strategies is important for effective planning to reduce risk to your operational performance. While short-term strategies provide immediate solutions to avoid disruptions, robust long-term strategies ensure sustainability and resilience. By integrating both approaches, companies can better navigate the complexities of obsolescence and maintain a competitive edge.
When asked about obsolescence considerations in inventory management programs, Matt Gallea provided both long-term recommendations and some short-term actions.
Long-term recommendations:
- Maintaining data regularly and ensuring bills of materials (BOMs) are up to date will improve forecasting for the end-of-life (EOL) parts required in your system.
- Proactive obsolescence management practices like predictive analytics, lifecycle forecasts, and scheduled obsolescence reviews are useful to anticipate obsolescence risk and better plan for potential upgrades, redesigns, and inventory.
- Keeping strong relationships with suppliers is integral to being well-informed on obsolescence risk.
- Consider flexible designs for component upgrades when designing systems for easy accommodation in the future.
Short-term actions:
- Last Time Buy: When notified by your supplier that a component is well on its way towards end of life, purchase enough components before they become discontinued to ensure adequate supply.
- Stockpile: Maintain a buffer stock of critical components with long lead times to cover immediate needs in case obsolescence arises.
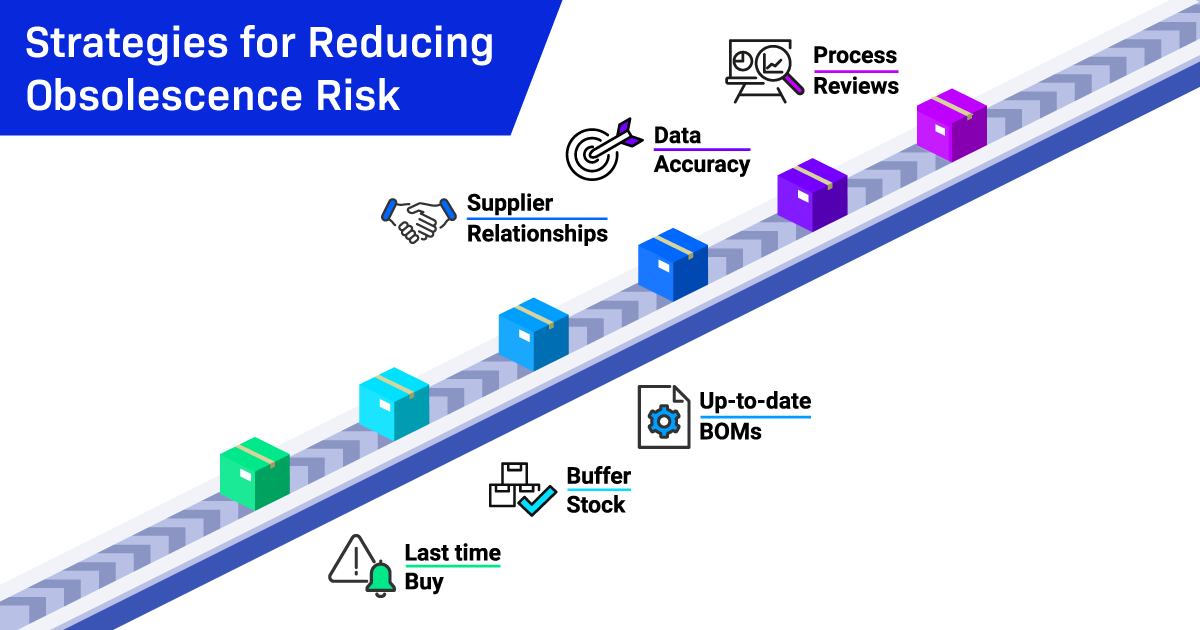
What compass are you using to address inventory management?
Staying ahead of obsolescence with an adaptive inventory management plan is essential to remain competitive in today’s evolving technological environment. To propel manufacturing operations forward intelligently, it is integral to recognize and understand the risk early. With the right information, manufacturers can be confident while planning longer-term initiatives like implementing effective upgrades or redesigns.
According to The Institute of Asset Management, “the development of a strategy to deal with aging assets (and obsolescence management) can help an organization to make the correct capital re-investment decisions and optimal timings. Given the complexity and significance of these cases, quantitative modelling, with decision support tools, is often worthwhile to evaluate options with uncertain patterns of degradation, risks, costs and consequences in order to find and justify the optimal investment decision and timing. At the portfolio level, asset investment decisions also need to consider new technology opportunities, obsolescence risks, stranded assets (through changes in functional demand) and repurposing opportunities.”
Today’s manufacturers must navigate a complex array of industry-specific factors when managing obsolescence. By focusing on regulatory compliance, supply chain stability, component lifecycle management, and design flexibility, companies can better mitigate obsolescence risk.
Matt Gallea advises manufacturers on some key industry and machine considerations to enhance operational efficiency:
- Regulatory compliance: Different industries have varying regulations regarding safety, environmental, and product standards. For example, the nuclear and medical device industries have stringent compliance requirements that must be met even as components become obsolete.
- Supply chain stability: Manufacturers need to ensure that their suppliers can provide long-term support and delivery of critical components on time.
- Component lifecycle: Electronic components typically have rapid technological advancements and shorter lifecycles vs. mechanical components.
- Customization and flexibility: When designing a system or product, it is important to consider flexibility to easily accommodate needed upgrades.
Broader obsolescence risk can impact the whole machine
Obsolescence in manufacturing and industrial operations is not just a matter of individual parts becoming outdated. The broader risks associated with obsolescence can impact entire machines, leading to significant operational challenges. Here, we explore some of the key risks and their implications:
- Safety risks: Obsolete components may not meet current safety standards, posing risks to workers and the production environment.
- Quality and performance issues: Using incompatible or outdated parts can compromise the quality and performance of the system, leading to product defects and reduced efficiency.
- Increased maintenance costs: As parts become scarce, the cost of maintaining and repairing machines increases. This includes higher prices for obsolete parts and the potential need for custom solutions and forced upgrades.
Relationships are crucial for successful operations
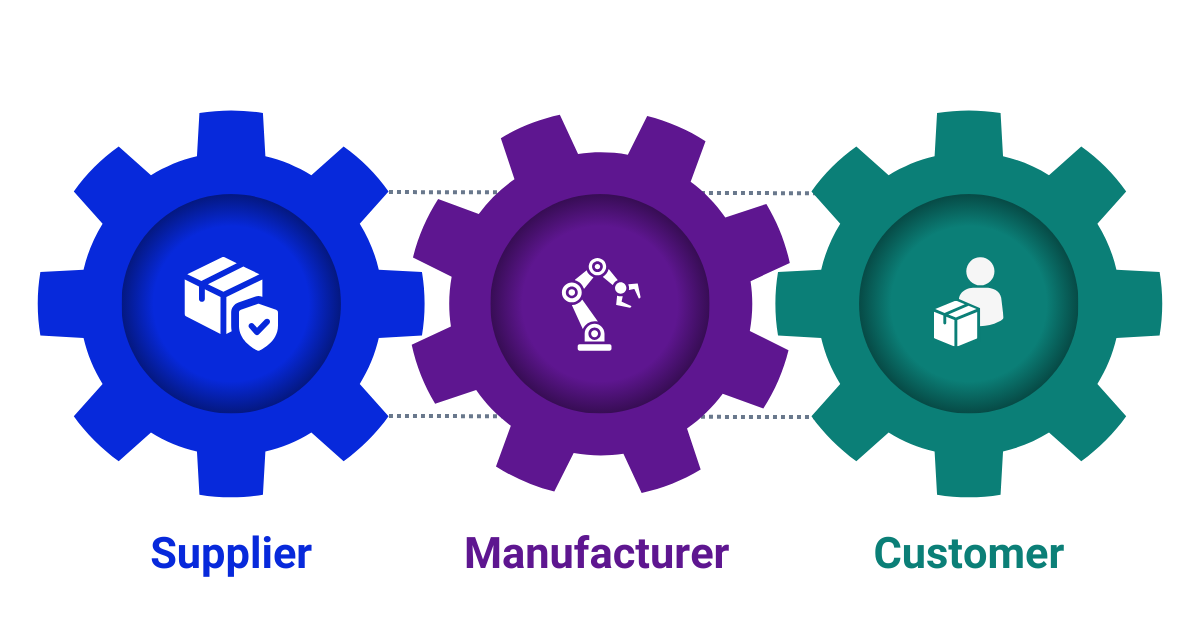
While it is essential to have a robust strategy for managing inventory, the relationships you cultivate with your suppliers and customers can significantly impact your operations. Downtime due to obsolescence can severely affect customer satisfaction. When you cannot fulfill customer orders because of inoperability resulting from outdated or unavailable parts, this dissatisfaction can strongly tarnish your reputation.
Effective communication with suppliers is vital to avoid obsolescence risk. Poor communication can result in suppliers not prioritizing your needs, leading to delays in lead times and further accelerating inventory issues. Building strong, transparent relationships with your suppliers ensures that your needs are met promptly and efficiently.
Using best practices will significantly reduce obsolescence risk
Having easy access to parts inventory information, while using proven techniques to identify and group items with greater priority and varying lead times, will improve forecasting and budgeting. This will also ensure that you are not wasting resources on less critical parts.
Get started on your obsolescence management by implementing the following inventory management best practices:
- Utilize inventory management software which enhances visibility and control over inventory.
- Categorize inventory based on asset criticality, part cost, and lead time.
- Forecast parts usage to help maintain optimum inventory levels.
- Maintain a safety stock of higher risk parts.
- Regularly conduct inventory audits to ensure records match actual stock levels.
This will not only streamline operations but also contribute to a more sustainable and profitable business model.
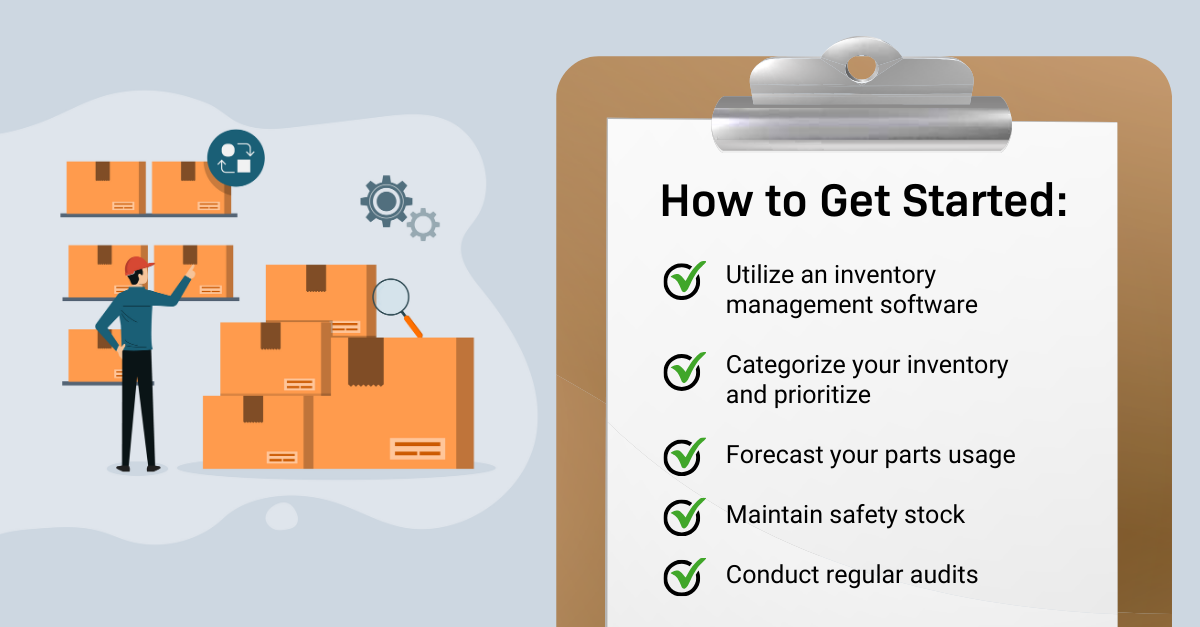
Closing thoughts
By adopting a proactive approach to obsolescence management, manufacturers can ensure smoother, more reliable operations. Implementing a comprehensive parts inventory management plan is essential. This involves balancing short-term solutions like maintaining buffer stock and making crucial last time buys, with long-term strategies such as regular audits, predictive analytics, and fostering strong supplier relationships. These measures help manufacturers prepare for obsolescence before it becomes a critical issue.
Understanding industry-specific factors, such as regulatory compliance and supply chain stability, further enhances a company’s ability to manage obsolescence risk effectively. By staying ahead of these challenges, manufacturers can maintain higher operational performance. Being prepared for obsolescence is not just about avoiding downtime—it is about ensuring the long-term resilience and competitiveness of your manufacturing operations.
So, what’s next for your manufacturing operations – risk or reason?
Let ATS design a parts inventory management program that meets your needs. Contact us today!
Sources:
International Institute for Obsolescence Management. “What is Obsolescence Management?” 2021.
The Institute of Asset Management. Asset Management – an Anatomy, July 2024, p.77.