Using Criticality Analysis to Optimize Your Operations
Mar 7, 2025
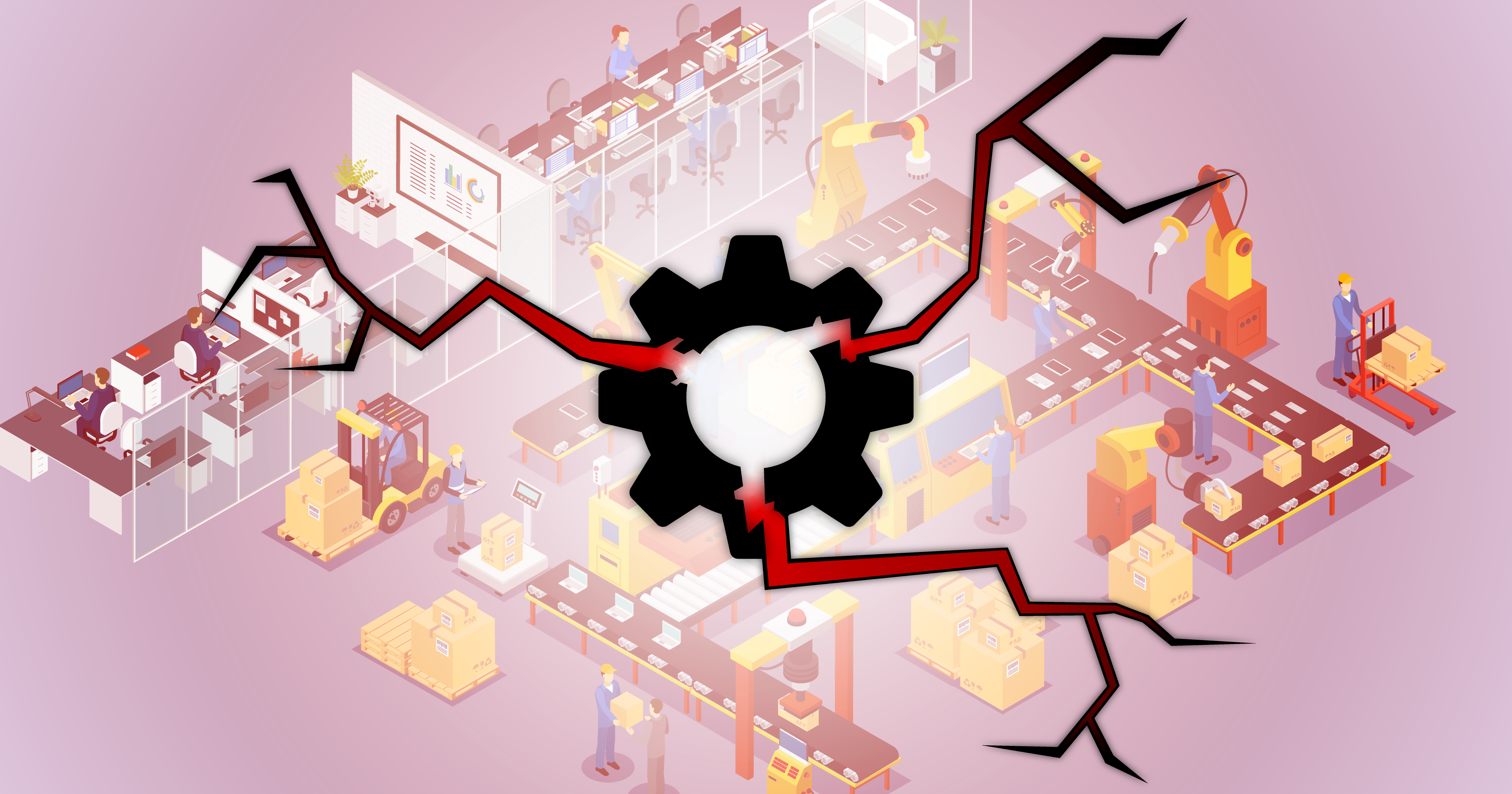
What are the most vital assets in your manufacturing operation? Your products will come out on top, of course, but the machinery and equipment that ensure their production and quality are likely to be a close second. Conducting a criticality analysis is largely about prioritizing and focusing time and effort on the capital equipment assets you’ve determined to be the most important in your operation. When they become damaged or unavailable, they will have a greater degree of severity on your production.
The criticality of an asset is determined by different factors, including its impact on product quality and ability to cause long-term disruptions. Obsolescence risks also play a crucial role, as outdated or unsupported equipment can increase downtime and create maintenance challenges, further impacting operational efficiency.
Critical assets are integral to the whole operation, from entire machines all the way down to the component level. If these assets are not functioning or accessible, they pose different risks to the integrity of the operation.
Andrew Espejo, General Manager of the ATS Reliability Center of Excellence and Triad Unlimited, has twenty years of experience working in the pharmaceutical industry. He advises that “criticality really is the descriptor of an asset and the role it plays in our manufacturing operations. Criticality helps narrow down where we’re going to spend our most valuable time analyzing and determining the risk.”
Factors for assessing criticality in your operation
When performing a criticality analysis, consider the following factors to ensure a proper assessment of your equipment:
- Identical assets throughout a site may not have the same criticality.
- Consider a chiller that is used to keep millions of dollars of food at a specific temperature and one that is used for an office area.
- Identify assets by importance of usage and where they are being used within the manufacturing process.
- Classify assets by type, operation, and manufacturer model.
Imagine preparing for a challenging expedition to the Arctic or Alpine regions. Prioritizing machinery like snowplows is integral to your expedition, clearing paths and making the terrain navigable. Heated shelters are also essential for maintaining the well-being of the crew. Each item plays a crucial role in ensuring safety and success, while each has different degrees of importance.
Where do your assets fit in this matrix?
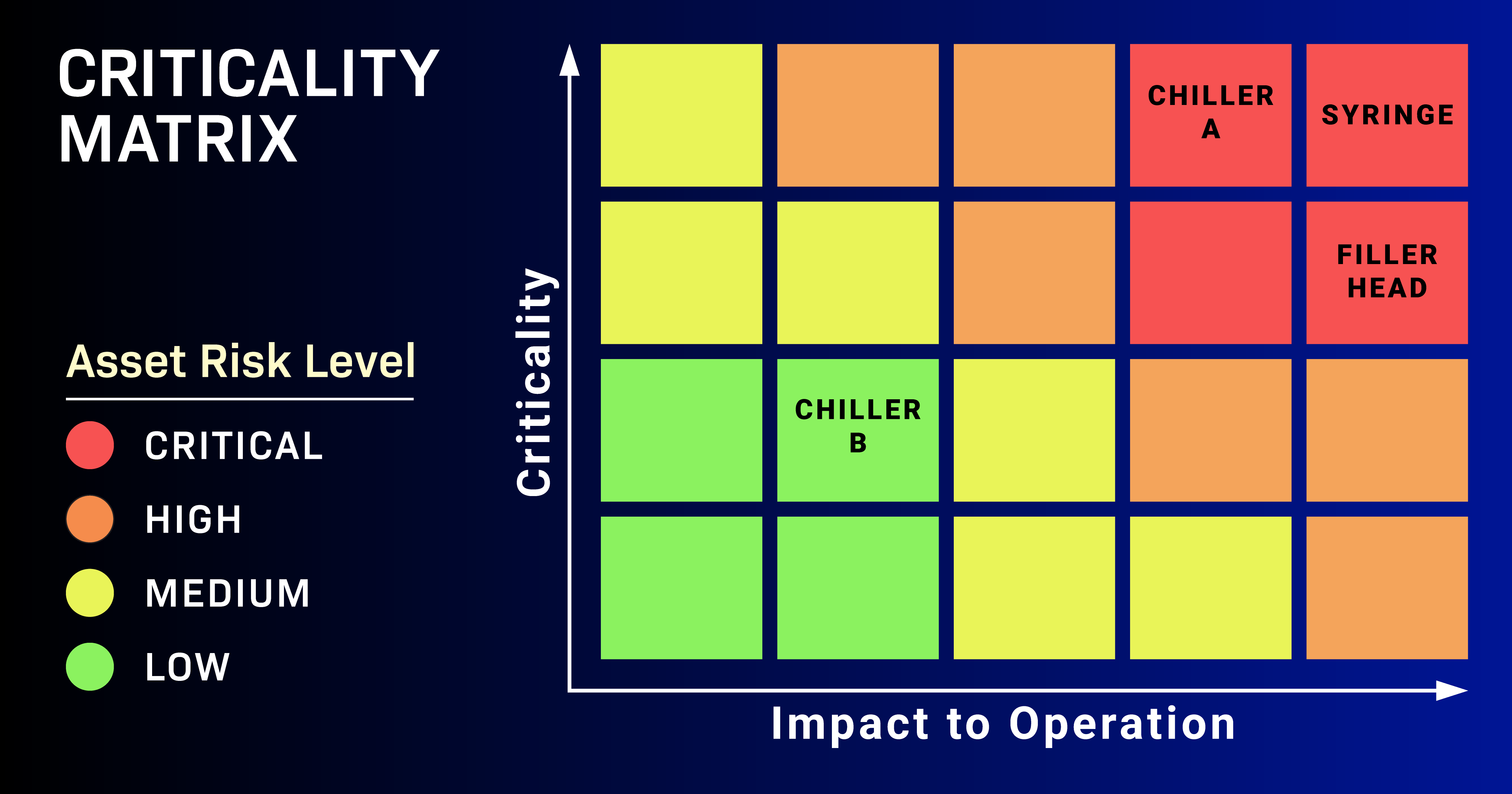
Not applying these principles can mean that manufacturers are not prioritizing the most important assets. This could lead to misdirecting manpower to address issues of less consequence and not focusing on issues requiring immediate attention.
If you’re considering risk-ranking the assets you have on site, here are some important criteria that your operations team should be looking at:
- Impact on process controls: critical components will likely have an impact on overall equipment effectiveness (OEE).
- Cost of critical components: look at repair costs as compared to actual value of equipment.
- Components with direct product contact: for example, filler heads for syringes can impact product quality and lead to lost batches.
Is your time well-spent on managing your assets?
Ranking assets based on their risk to your operation is important to understand overall production risk and ensure consistent performance. These considerations can better direct operational decisions like determining which assets will take priority in a predictive performance assessment or a Failure Mode and Effects Analysis (FMEA) that assesses when an asset is likely to fail. A good understanding of which critical components are likely to affect operational sustainability is integral to criticality analysis.
Identify when critical assets are likely to cause a disruption
- When a component is most likely to fail
- When an asset reaches a certain temperature
- The number of production cycles (wear and tear)
- Long lead times
- When the asset is becoming obsolete or is reaching end of life (EOL)
In the pharmaceutical and food industries, machines must adhere to strict regulatory requirements by maintaining a validated state. If an asset jeopardizes this, it’s likely to be considered critical by risking those standards.
Wayne Cosby, Manager of Quality Assurance at Triad Unlimited, has held several positions throughout his career including Navy Nuclear Electrician, Navy Diver, Technician, and Maintenance Supervisor. He has a fundamental understanding of identifying critical assets and how to manage them.
From Wayne’s experience as an electrician on a fast-attack submarine and as a Navy Diver, he advises:
“Performing a criticality analysis is the difference between going up and down. It becomes a life-threatening kind of situation if you don’t understand what assets are critical and what assets need to be maintained, in order to determine which direction you’re going to go. This puts life in jeopardy, if you’re not maintaining critical equipment.”
Wayne Cosby, Manager of Quality Assurance, Triad Unlimited
Asset criticality is vital to your manufacturing operation
Preparedness lends a hand to employee confidence – fixing one failure after another takes a huge toll on employee morale. Instead of chasing fires, use asset criticality to spend more value-added time on processes and improve your operational strategy. Knowing and understanding your critical assets gives operations teams the ability to focus their attention on high-risk functions.
The study in Advances in Production Engineering & Management (APEM) Journal provides insights regarding the benefits of understanding criticality for Engineer-to-Order (ETO) manufacturing:
“Consistent issues include production scheduling, planning and control, efficiency, and lead time reduction. The criticality analysis enables ETO companies to understand problem implications and prioritize decision-making and resource allocation. Addressing the significant criticality problems will minimize negative consequences on ETO project success.”
Take these steps to apply asset criticality to your operation
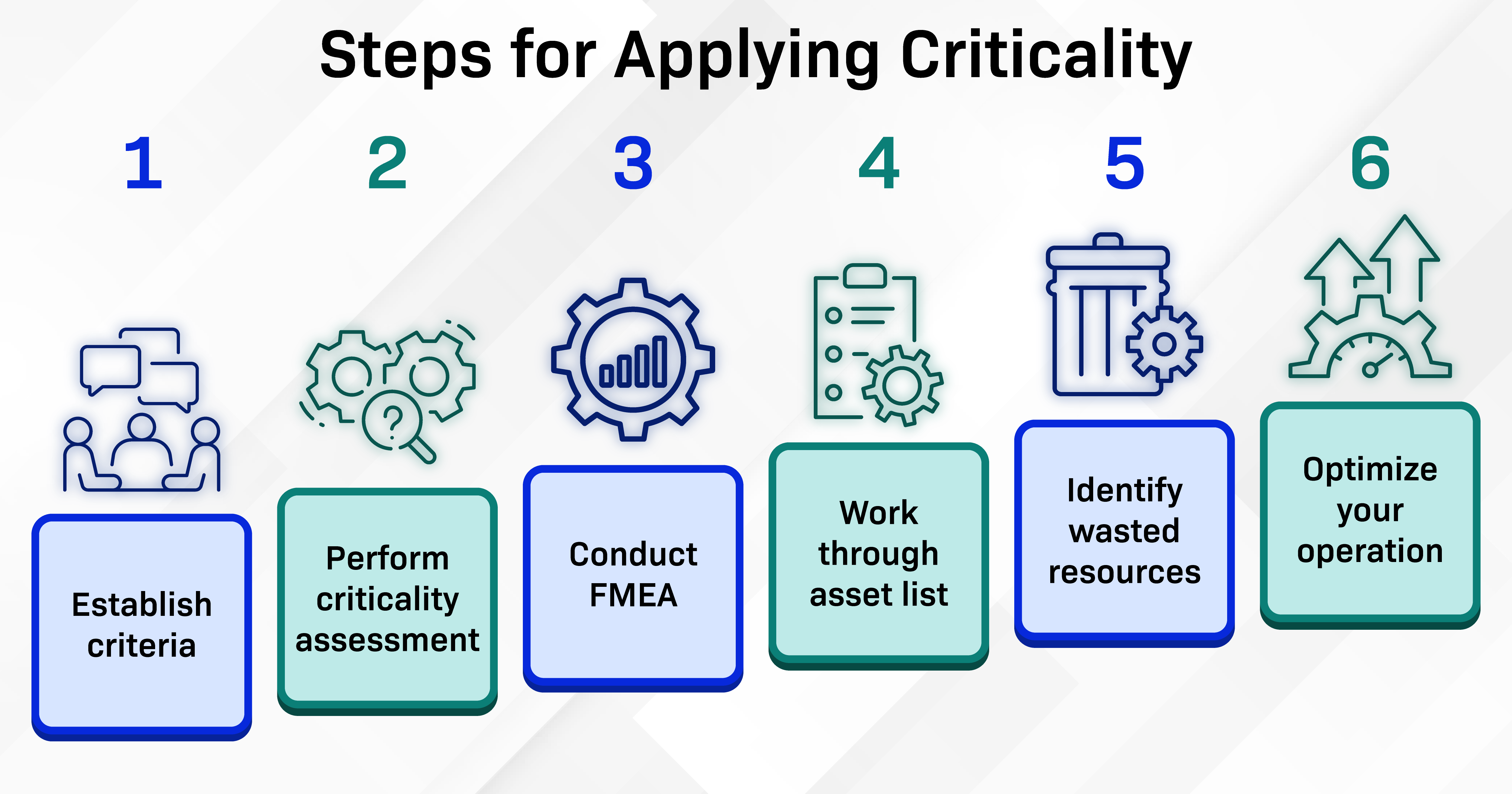
Use the following areas to analyze the criticality of your equipment and improve your manufacturing operations:
- Establish criticality criteria for your assets: function, repair time, operational impact, replacement cost, and SME requirements.
- Perform asset criticality assessments on all assets at the site.
- Conduct a Failure Mode and Effects Analysis (FMEA) starting with your most critical assets.
- Work your way through the asset list.
- Identify areas where you may be wasting resources, like spending too much maintenance time on less critical parts or randomly replacing an asset.
- Optimize preventive maintenance strategies based on these assessments.
The time required to establish the criteria and complete a criticality analysis for a manufacturing operation varies based on the site’s size and the number of assets involved. Without a dedicated reliability team, it can become an extremely challenging and time-consuming process. Resource allocation plays a crucial role as the process demands continuous attention and effort to record and document information.
Andrew Espejo advises, “All the stakeholders have to be engaged in the process: the maintenance technicians, the supervisors, and the operations team. That’s where many organizations get tripped up, because they think it’s just being done by maintenance, but they can’t do it alone.”
Let’s change the conversation to asset criticality
Asset criticality is a core principle of reliability engineering. In Andrew Espejo’s experience, there has been too much focus on maintenance and little awareness of reliability principles like criticality, resulting in low adoption of this strategy by plant managers.
The Global Forum on Maintenance and Asset Management takes an in-depth look at integrated reliability:
“Integrated Reliability deploys, develops, and designs policies, procedures, and processes to support reliability, availability, and maintainability. The organization should identify and develop Asset Management strategy programs to manage the consequences of failure based on failure modes, operating context, criticality, risk and identified task effectiveness. It should also analyze maintenance, repair, and operations (MRO) spares for criticality, redundancy, and required quantities.”
Andrew also states, “If you took a hundred general managers and put them in a room and started talking to them about reliability, I’d say three out of those hundred would get it. If you change the conversation to throughput and uptime, you’ll have everybody’s attention.”
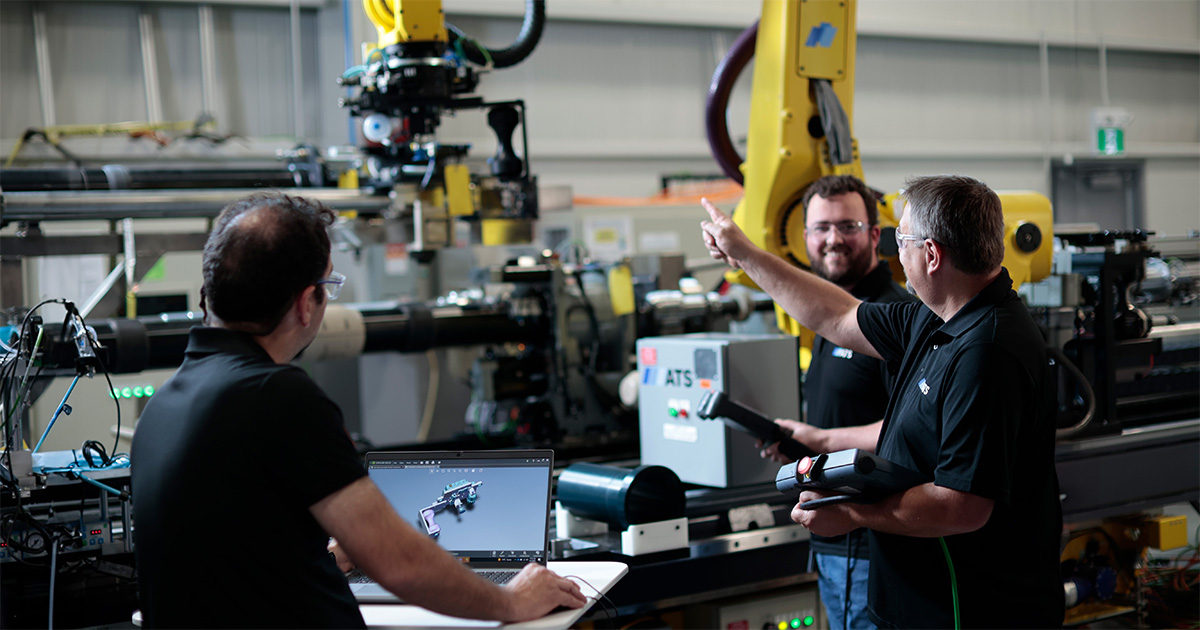
Now that you’ve identified your most critical assets
- Optimize the use of labour by directing your maintenance schedule towards more critical areas of your operation.
- Opt to schedule physical inspections more often.
- Consider ‘running to failure’ for low impact assets.
- Rebuild equipment at defined intervals, depending on the criticality of the equipment.
- Use predictive or condition-based maintenance to identify the onset of failure.
Based on your criticality analysis, Andrew Espejo informs that “a Failure Modes and Effects Analysis (FMEA) can determine the conditions at which a critical component will fail. This will help manufacturers decide whether to invest in monitoring these conditions.”
This type of analysis will influence decisions like whether you want to perform invasive or predictive maintenance. Manufacturers can also decide whether to investigate if issues are caused by the upstream process or the component itself.
FMEA examines failures by determining:
- Severity: Does the failure impact functionality of the asset and is it still within standards?
- Likelihood: How often would we expect to see that failure mode occur?
- Detectability: How is the asset monitored: by operator, technician, or monitoring system?
FMEA identifies component failures in areas including:
- Number of cycles
- Specific temperature
- Pressure and flow rates
- Vibration
Use condition-based monitoring for proactive maintenance
Today’s advanced management systems are designed to take data from a machine to notify operations teams that an asset is close to failing. This knowledge is especially important for critical components. This information can come from the machine’s sensors that send a signal to generate a work order in the Computerized Maintenance Management System (CMMS). Condition-based monitoring identifies when an asset needs attention and informs manufacturers that it requires ordering, replacement, or maintenance.
These trigger points and failure information give you the ability to schedule maintenance, like unplanned downtime, with flexibility and more control over your operation. Operations teams can also use this information to identify long-term trends affecting their operation and make better decisions regarding machine upgrades or redesigns.
Closing thoughts
You may be asking yourself the question—is this approach sustainable? The answer is yes! When introducing a new asset to your operation, it’s imperative to keep in mind that a variety of people and departments are going to be involved in implementing criticality. For example, when purchasing new capital equipment or other critical assets, buyers are likely to spend more time researching innovations or obsolescence risk. Also, finance teams will spend value-added time prioritizing critical assets and making more room in their budgets. Operations and maintenance teams will know when and how to perform tasks and work processes based on what they’ve identified as having the highest risk to manufacturing operations.
When manufacturers decide to implement asset criticality practices, it is important to understand that this is a long-term investment that needs to be embedded in every aspect of your organizational culture. This approach changes the way everyday problems are solved, and by prioritizing them, this makes managing them much more meaningful. If you decide to invest in using criticality analysis to reduce operational risk, ensure this process stays integral to the functioning of your operation so that it can thrive with time well spent.
Explore ATS reliability engineering services or contact us today to learn how criticality assessments can improve your operation.
Sources:
Fortes, C.S., Tenera, A.B., Cunha, P.F., and Teixeira, J.P. “Engineering-to-order manufacturing: A criticality analysis of key challenges and solutions based on literature review.” Advances in Production Engineering & Management 18, no. 2 (2023).
The Global Forum on Maintenance & Asset Management. The Asset Management Landscape, June 2024, p.74.